ERIE, PA (April 7, 2022). Plastikos began working with RJG in 2009 when the electrical connector market was the bulk of their business model. Due to the small piezo sensors RJG offered, their equipment looked to be a good fit for Plastikos’ modular tooling. When these sensors were introduced and the tooling retrofitted, RJG worked alongside the company to ensure success. As Plastikos expanded into medical device markets and Plastikos Medical came online, the relationship with RJG simultaneously grew to implement various sensors into medical molds. Today, the relationship continues to be strong.
Danielle Bentley, Plastikos Medical’s Medical Molding Manager was eager to express gratitude for the Mold Smart Award’s nomination process. “We were very honored to hear we won the first RJG Mold Smart Award. Filling out the application was eye opening to us. We knew our downtime and scrap had gone down over time, but we did not realize applying the eDART and implementing training had such a high impact on our processes. When I saw the dramatic drop in scrap and press downtime the year after we implemented eDART as well as another drop when I started teaching RJG classes in-house in 2016, it validated RJG’s technology and courses.”
“As an RJG Qualified Trainer, it is a remarkable feeling to see within our metrics that Process Technicians are taking the skills they learned in their classes and are applying it while on the molding floor. When I started seven (7) years ago, we had so many jobs that required an operator full-time to catch defects. Now more jobs are able to be automated because of this, and one operator can handle multiple presses during their shift.”
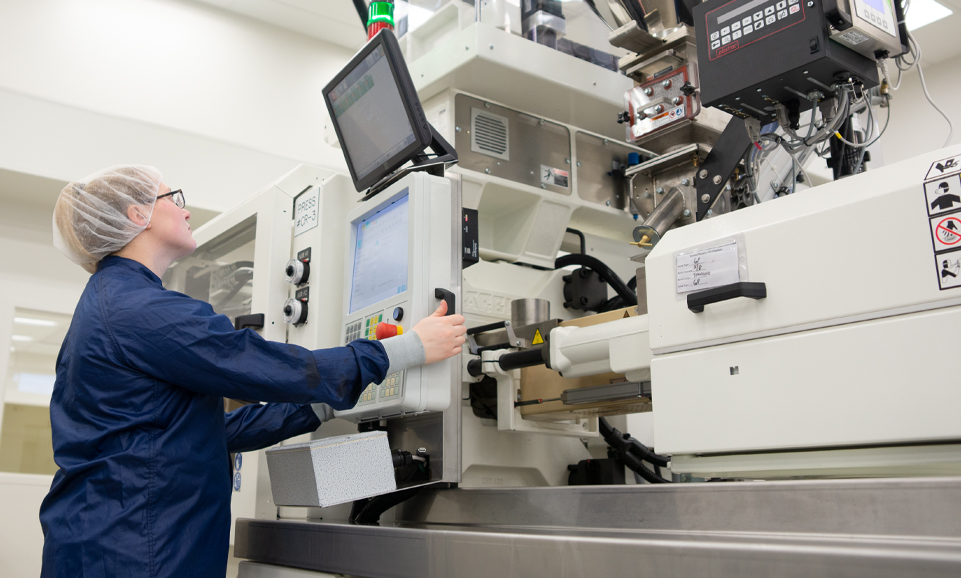
Utilizing RJG’s eDART technology, coupled with training course implementation, has led to reduced scrap rates, reduced downtime, and ultimately fewer external rejects reaching the customer. Plastikos & Plastikos Medical can identify problems quickly by using templates made during the qualification process and the cycle graphs to pinpoint where in the cycle problems are occurring.
External PPM continues to drop annually by using the eDART to monitor the process and remains low today. Automatically sorting for defects using the eDART system and cavity separation methods has ensured that only acceptable parts are sent to our customers.
RJG sensors have been retrofitted on many existing molds and have been added to almost every new mold being built by Micro Mold – Plastikos’ & Plastikos Medical’s sister company. Customers are starting to see the benefits of this as external PPMs continue to decrease.
Nick Schroeck, Plastikos’ Sr. Process Engineer further explained, “Since implementing the technology in 2009, we have shipped nearly four (4) times more parts per year, while decreasing the external scrap PPM by 96%. That is pretty amazing.”
About Plastikos, Inc. & Micro Mold Co., Inc.:
Based in Erie, Pa., Micro Mold & Plastikos specialize in precision mold design & fabrication as well as tight-tolerance injection molding. Plastikos Medical came online in 2019 and is 100% dedicated to supporting the Medical OEM customer-base. With over 100,000+ square-feet of combined mold design & fabrication, engineering, as well as cleanroom and white room manufacturing space, our primary fields of expertise relating to plastic manufacturing include medication delivery systems, surgical eye care, microfluidic, and electronic connector, among others. Our medical molding rooms are controlled through two ISO 7 cleanrooms and one ISO 8 cleanroom.